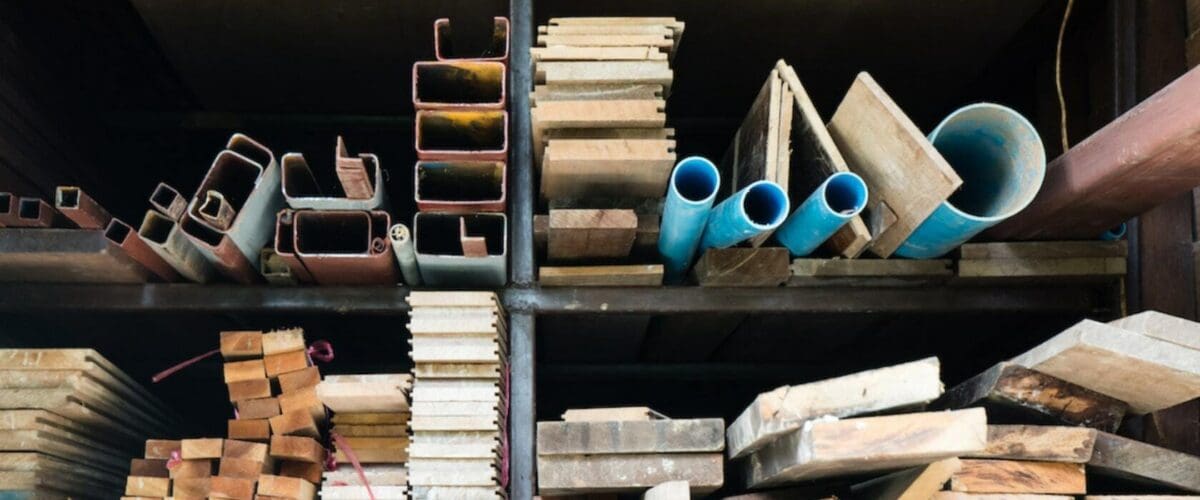
Raw material costs are escalating sharply since 2021. Global markets shrouded in the uncertainty of the COVID-19 pandemic has seen steel, cotton, rubber, copper, cruise oil and lumber prices surge to a level we haven’t seen in a long time. We’ve all felt the impact. It’s costing more to produce goods, meaning the price of the products we make are being passed to consumers. Whether it’s cutlery for the kitchen or the newest building in New York, inflation is causing a squeeze for consumers all around the world.
Despite U.S. stimulus, European openness and vaccines spreading to every corner of the globe, there doesn’t seem to be any sign that raw material costs are decreasing. So why are raw materials rising so steadily in 2021, and how can businesses possibly tackle the impact? Below, we seek to answer those two questions.
Why raw material costs are increasing
There are a range of reasons behind the intense rising costs of raw materials, but it all boils down to the unparalleled impact of the pandemic. Starting in 2021, and continuing well into 2022-2023, COVID-19 has put nothing but upwards pressure on numerous costs throughout the supply chain.
Strong market demand
Global economic recovery, and a rapid reopening, has contributed to the increase rise in raw materials. The OECD estimates growth to reach 5.7% in 2021, and 4.5% in 2022 (although strength will differ considerably across different countries).
The pandemic has massively changed the way people shop. People – suddenly facing movement restrictions and lockdowns – flocked to online shopping in droves, turning to eBay, Amazon, UberEats and other Ecommerce platforms for their shopping needs. Sharp global demand has meant more and more raw materials are needed to build the essential products we need, and the packaging it comes in (whether it be cardboard, bubble wrap, tape or air bags).
Chinese economic recovery
The surging recovery of China’s economy plays a massive role behind the skyrocketing of raw material prices. The world’s most powerful economy is building itself up again after the unexpected calamity it faced in light of COVID-19. Their production was up by about 6.9% year on year in October 2020, much quicker than other places in the world such as Europe.
The result has meant the Chinese economy is starving for raw materials, especially as their manufacturing industries scurry to meet global demand for products.
Green energy revolution
A transition away from fossil fuels to more eco-friendly alternatives has also contributed to these increasing prices. For example, a surge in demand to build power grids has come with rising prices for copper. In fact, around 1.9 million tonnes of copper were used to construct electricity networks that year, and copper prices rose about 21% earlier in 2021.
Other raw materials needed to build solar panels like PV glass and silver paste have increased, resulting in solar module costs to increase by 35%.
Global container shortage
The rise in raw material costs has also been driven by an international container shortage. Containers are literally piling up in ports around the world where they are not needed, and businesses are struggling to secure the vital boxes they need to import or export their goods. They’re also stranded at sea, as vessels wait days to unload ever-congested ports. As a result, these steel boxes are more difficult to locate than ever before.
This has contributed to massively increased shipping costs, including a tripling of costs to ship between China and Europe. Indeed, the costs of transporting one single 40-foot container on a route ballooned from USD $2,000 to over USD $9,000 according to some importers.
The container shortage has created pressure on all prices, including the prices of raw materials, as shortages creates struggles for importers trying to get the goods they need.
Brexit trade barriers
After the United Kingdom formally left the European Union, new trade restrictions have contributed to pushing up the costs to purchase taw materials. Some of these new barriers have included new rules of origin requirements (including for raw materials) and burdensome customs processes. Around 65% of manufacturers in the UK alone reported higher costs.
Timber shortages
Softwood materials are very difficult to come by nowadays. This has only been made worse by poor weather, licencing issues and timber infestation in some of parts of the world. The strain has been particularly felt with the increase in demand for home improvement, DIY and construction materials in the face of lockdown.
It explains why the prices of lumber have increased to over 75% of pre-COVID levels.
How to address the impact of rising raw material costs
The best thing that shippers across the world can do in the face of ever surmounting raw material prices is adapt. Below, we’ve outlined some tips on how you can keep within your profit margins in the face of rising production costs throughout your supply chain.
Reduce the scrap
One of the most effective places to start doing right away is to streamline the use of the raw materials you’re currently using.
You would be surprised how much raw material wastage (in other words, ‘scrap’) eats into your production costs. For example, the value of scrap waste from food and food products manufacturing in Australia alone was valued at $158 million in 2017. A simple alteration of a product design or change some of the ways you make your products, taking into account units of raw material, could potentially lower any excessive scrap you may be creating.
Leverage suppliers
Another way to potentially reduce costs is to leverage your suppliers and get the most affordable partner you can find without sacrificing the quality of your product. Searching for suppliers with faster delivery times, more affordable shipping costs and reduced costs for services is certainly can pay dividends – especially if it means an improved bottom line.
Use a professional sourcing company to reduce costs
As prices rise exponentially through supply chains across the world, it is prudent to have a reliable sourcing company and freight forwarder by your side. If you’re in the business of manufacturing products from raw materials, our team at Tactical Sourcing is dedicated to finding the right suppliers for you and negotiating the best possible deal.
Tactical Sourcing are experts in the industry, and our freight forwarding team can help streamline your shipping processes and improve your company’s profitability.
So get in touch with our team today to discuss your supply chain, and we can help you adapt to the ongoing unpredictable rise of raw material costs.
The TSC Team,