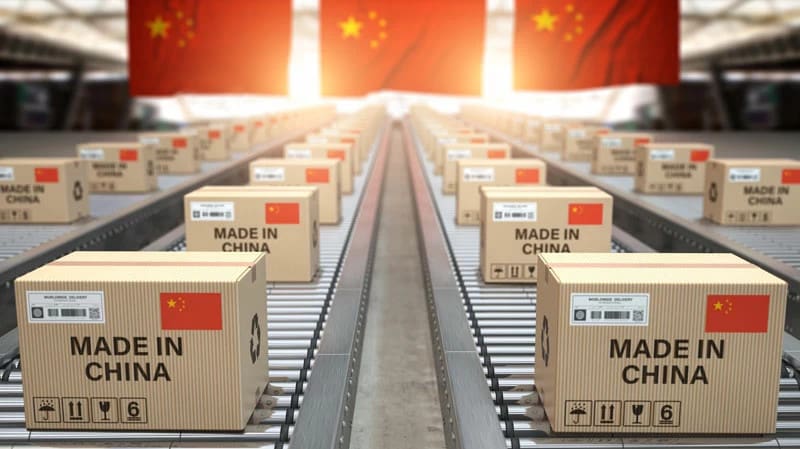
Outbreaks of COVID-19 and geopolitical tensions underscore the urgent need to look beyond costs and diversify production to alternative locations to lower the risk of disruption
Multinationals including Apple and Tesla are facing severe disruption to their supply chains in China after Beijing eased its stringent COVID-19 rules and infections swept across the country, underscoring the risk of concentrating production in one location.
With China’s relative advantages as a cheap manufacturing hub waning, more international groups will be looking at diversifying production to alternative locations. A wider geopolitical decoupling also threatens global trade, so executives should be finding ways to improve the resilience of the supply chain – not just lower costs – to ensure it does not snarl. Global organizations can consider these five ways to cut supply chain risks in the wake of China’s nationwide outbreak of COVID.
Spread sourcing and production to improve resilience
The rapid dismantling of COVID restrictions in China is further diminishing its attractiveness as the world’s factory, coming on top of escalating tensions with the US. Companies from Meta to Google had already made plans to move at least some production and sourcing out of the country following the trade war that kicked off under Donald Trump’s presidency, as it increased tariffs. Dell plans to stop using computer chips made in China by 2024 and reduce other “made in China” components in its products.
The Biden administration is now trying to reduce US firms’ supply chain dependency on China. For example, the US has launched controls that restrict exports of technology to Chinese semiconductor manufacturers. The controls even hit some companies in Europe, underlining the unpredictable nature of geopolitical risk.
China’s COVID surge adds to the concerns facing multinationals. After outsourcing production to cheaper offshore locations, fueling a three-decade era of globalization, many companies are looking at bringing production back closer to home in a nearshoring push.
This also reflects the fading advantages of China as a manufacturing base, as wages in the country have more than tripled over the last decade, making it far less competitive than cheaper locations in Mexico and elsewhere. Supply chain risks have also increased. China’s exports plunged 9.9% in December, the sharpest fall in nearly three years, as global demand slackened and COVID spread. In response, companies should be preparing alternatives for assembly and production beyond China – ideally in multiple countries such as India, Vietnam, and Taiwan to improve the resilience of sourcing and production.
Localized production in China, for China
Multinationals are not advised to pull out of China entirely, because it remains a huge market in which to sell as well as produce goods. In the short term, economic activity has slowed because of COVID, with retail sales and factory output falling in December. Carmakers including Tesla and Mercedes-Benz have slashed vehicle prices in China – a further sign that demand is softening.
But the lifting of curbs has raised hopes for a rebound in China’s consumer activity, which was muffled by recurrent lockdowns. That optimism strengthens the case for localized production in China, with multinationals producing goods that are only used in the world’s second-largest economy.
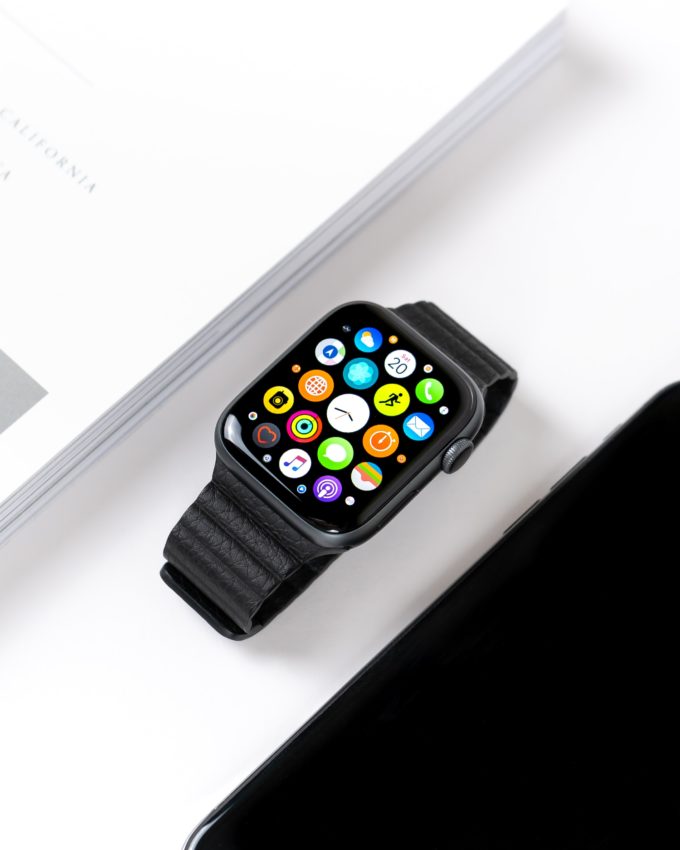
“China for China” has now become a common phrase in corporate circles, as it reduces dependency on Chinese factories for exports while keeping a stable local supply chain to service the Chinese market. For example, the pharma giant AstraZeneca has opened an inhaler manufacturing facility in the city of Qingdao. Schneider Electric, the energy management company, has R&D hubs in China where it makes a product that controls energy usage, designed for the Chinese market and exported elsewhere in Asia.
Locate savings to protect margins
Nearshoring can be a more expensive option than offshoring, pushing up the costs of both labor and material. This means companies need to find savings elsewhere to preserve their margins. With consumer confidence low around the world, they are unlikely to pass on the full costs to customers without suffering a fall in volume.
Manufacturers have been hit by soaring energy prices, even as milder temperatures in the northern hemisphere have eased worries about power shortages in Europe. Finding ways to further lower energy costs should be a priority; expanding use of renewable power to meet climate targets and cut dependence on Russian energy, for example, even as rising component prices limit renewable capacity.
Companies are also switching to cheaper or more widely available components to make their products. For example, some companies are avoiding alloys that are difficult to find and using relatively standard steel. While it is not the same performance, it is good enough.
Take greater control over the supply chain
However, as well as looking for immediate cost savings, firms should be focused on the resilience of their supply chains to ensure stability of production. That can involve trade-offs that drive up costs today but promise greater returns in the longer term.
Many companies have, for instance, been using more flexible and short-term contracts with suppliers to adjust to changes in customer demand. But I recommend signing longer-term contracts with their key suppliers to build additional resilience in the supply chain.
On top of that, “in-sourcing” is becoming a wider trend as companies including Apple begin to take greater control over their supply chain. The tech giant is planning to use its own screens for the iPhone and Apple Watch, Bloomberg has reported. It currently uses displays from suppliers including Samsung and LG. The move would streamline production and make Apple less dependent on external companies to make key products that drive the group’s sales.
Corporate standards to protect employees
As China reverses its zero-COVID policy, the medium-term risk is that of worker shortages at factories and warehouse, distribution, logistic and transportation facilities, wreaking havoc on supply chains. Modeling suggests that a million Chinese people are at risk of dying from COVID as the pandemic controls are eased. The worker shortages are being compounded by the lunar new year, with many migrant workers heading home for the holiday this weekend.
The COVID outbreaks at Chinese factories underline the importance of good corporate standards to protect employees in order to keep production humming. Apple’s manufacturing partner Foxconn suffered an outflow of workers attempting to escape a COVID outbreak and avoid being locked down, hitting production and limiting supply of Apple’s newest high-end iPhones.
Companies wishing to avoid a similar fate should be keeping employees safe while taking steps to control more of their supply chain, on top of finding savings and diversifying production bases to avoid the supply chain breaking down. Those steps will ultimately lessen the reliance on China as the world’s factory. Given that it takes time to switch sourcing and production to another country, and it could prove expensive, the supply chain shake-up is likely to prove permanent.
Our team at Tactical Sourcing is dedicated to finding the right suppliers for your production in Vietnam and negotiating the best possible deal. We are experts in the industry, and our freight forwarding team can help streamline your shipping processes and improve your company’s profitability.
So get in touch with us today to discuss your production plan, as you begin your sourcing journey in the Vietnam market
The TSC Team,